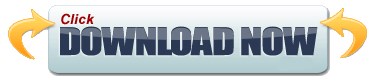
When the stop button is pressed, contact TD 1 waits for the specified amount of time before returning to its normally-closed state, thus holding the reverse pushbutton circuit open for the duration so M 2 can’t be energized. This being the case, the normally-closed, timed-closed contact of TD 1 between wires 8 and 5 will have immediately opened the moment TD 1 was energized. If the motor has been running in the forward direction, both M 1 and TD 1 will have been energized. What we want each time-delay contact to do is to open the starting-switch leg of the opposite rotation circuit for several seconds, while the fan coasts to a halt. If we use contacts that delay returning to their normal state, these relays will provide us a “memory” of which direction the motor was last powered to turn. Let’s begin by adding a couple of time-delay relay coils, one in parallel with each motor contactor coil. What we might like to have is some kind of a time-delay function in this motor control system to prevent such a premature startup from happening. If the fan was still coasting forward and the “Reverse” pushbutton was pressed, the motor would struggle to overcome that inertia of the large fan as it tried to begin turning in reverse, drawing excessive current and potentially reducing the life of the motor, drive mechanisms, and fan. This could be problematic if an operator were to try to reverse the motor direction without waiting for the fan to stop turning.
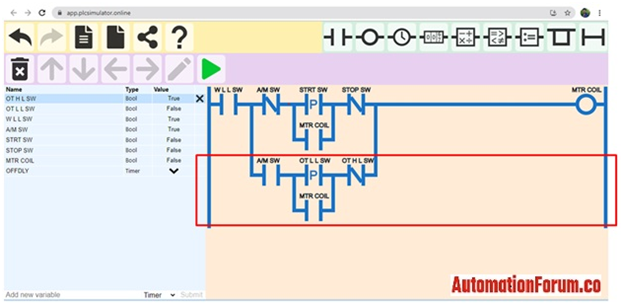
If our hypothetical motor turned a mechanical load with a lot of momentum, such as a large air fan, the motor might continue to coast for a substantial amount of time after the stop button had been pressed. Let’s consider another practical aspect of our motor control scheme before we quit adding to it. The “Stop” switch, having normally-closed contacts, will conduct power to either forward or reverse circuits when released. Now, if either forward or reverse circuits are latched, they may be “unlatched” by momentarily pressing the “Stop” pushbutton, which will open either forward or reverse circuit, de-energizing the energized contactor, and returning the seal-in contact to its normal (open) state. To stop either circuit (forward or backward), we require some means for the operator to interrupt power to the motor contactors.
#VACUUM CHILLER LADDER LOGIC PROGRAM HOW TO#
However, this creates a new problem: how to stop the motor! As the circuit exists right now, the motor will run either forward or backward once the corresponding pushbutton switch is pressed and will continue to run as long as there is power. These parallel auxiliary contacts are sometimes referred to as seal-in contacts, the word “seal” meaning essentially the same thing as the word latch. The same sort of thing will happen when the “Reverse” pushbutton is pressed. When the pushbutton is released, the closed M 1 auxiliary contact will maintain current to the coil of M 1, thus latching the “Forward” circuit in the “on” state. When the “Forward” pushbutton is actuated, M 1 will energize, closing the normally-open auxiliary contact in parallel with that switch. Let’s see how the second approach is implemented since it is commonly used in industry:
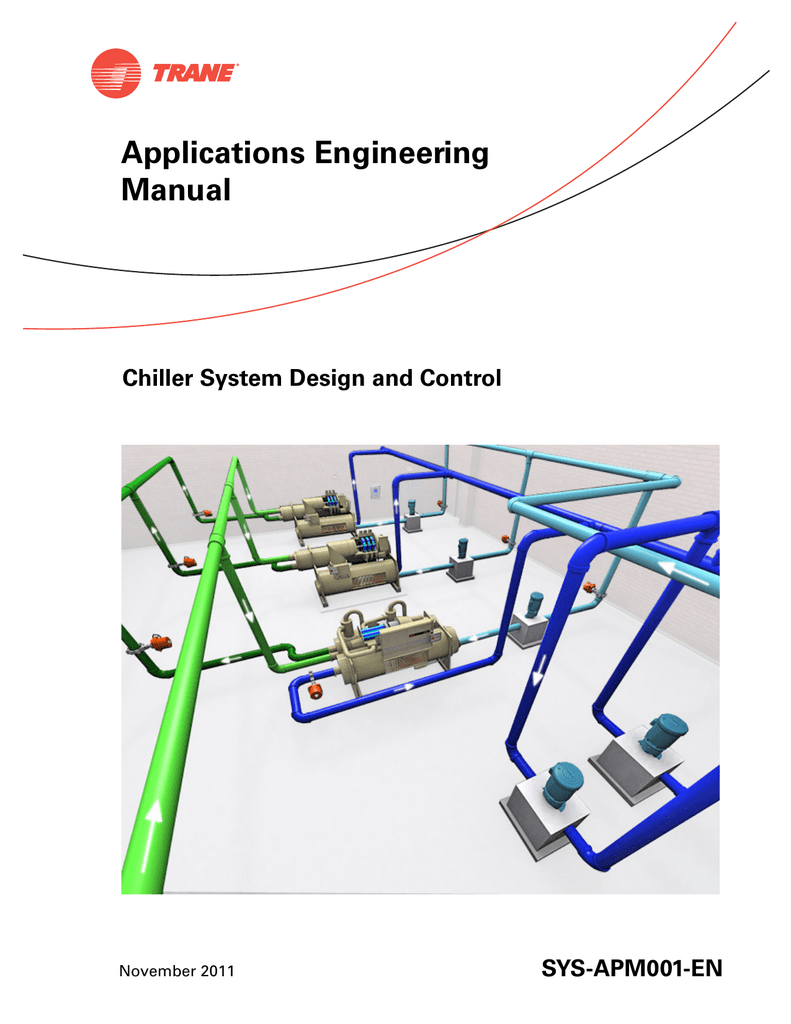

If we wanted to keep the motor running even after the operator takes his or her hand off the control switch(es), we could change the circuit in a couple of different ways: we could replace the push button switches with toggle switches, or we could add some more relay logic to “latch” the control circuit with a single, momentary actuation of either switch. The interlock contacts installed in the previous section’s motor control circuit work fine, but the motor will run only as long as each push button switch is held down.
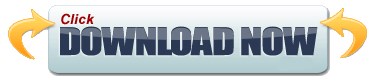